Earn your 30-hour Cal/OSHA completion card with five days of in-depth training.
Benefits of Pryor Learning training versus OnDemand options.
- Award-winning and OSHA-authorized training.
- Live Virtual Instructor-Led Training (VILT) with ample Q&A time.
- Tailored learning speaks directly to individual and organizational needs.
- Select invoice option for deferred payment if more than 7 days prior to event.
- DOL card issued in accordance with attendance and eligibility.
- Pryor offers fast and efficient OSHA training taught by an OSHA Outreach Training Program Authorized Trainer.
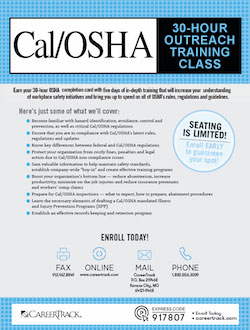
Earn your 30-hour Cal/OSHA completion card with five days of in-depth training.
This program provides five days of in-depth training guaranteed to increase your understanding and awareness of workplace safety initiatives. Get up to speed on major California CRR Title 8 rules, regulations, and guidelines. Upon successful participation, you receive an OSHA Course Completion Card.
Download BrochureRequirements
- A tablet, laptop or desktop computer with keyboard, video camera and microphone capabilities.
- Attendees must participate and be visible to the entire class for all of the 5-day training event.
- Internet connection, broadband wired or wireless (3G or 4G/LTE).
- 2-way audio: speakers and a microphone – built-in or USB plug-in or wireless (note: students can use the microphone and speakers built into a tablet, laptop or desktop computer. Headphones or earphones with a microphone are also recommended, but not required.)
- 2-way video – built in or USB plug-in video web camera (note: students can use the video camera internal to their device or use an external device).
- PDF viewer on device.
- Smartphones will not be permitted as a device to attend the virtual session.
Earn your 30-hour Cal/OSHA completion card with 5 Days of Virtual Instructor-Led Training !
This General Industry Outreach Training Program provides five days of in-depth training guaranteed to increase your understanding and awareness of workplace safety initiatives. Get up to speed on all major California standards, regulations and guidelines including CRR Title 8, IIPP, form 300 and more. Upon successful participation, you receive an Cal/OSHA Course Completion Card.
Safety and health training isn't just a bureaucratic exercise - it may save your life or the life of a co-worker. Plus, these valuable skills help you to meet stringent job requirements or give you the edge you need in today's tough employment market.
Are OSHA violation and workplace safety issues costing your organization?
According to the United States Department of Labor, businesses spend $170 billion a year on costs associated with workplace-related injuries and illnesses. Occupational illness and injury contribute to decreased employee morale, reduced productivity and higher on-the-job stress, while leading to increased worker's comp claims, higher insurance premiums, retraining costs, absenteeism, and lower-quality products and services.
Workers whose employers take steps to protect their health, fitness and safety on the job are more likely to report job satisfaction, enjoy a higher quality of life, contribute a more optimistic, enthusiastic outlook, and interact positively with their work peers and superiors.
Welcome and Overview of the Week's Training
- Employers covered by the Cal/OSHA Act
- Exclusions from coverage
- Cal/OSHA Training Institute Introduction to Cal/OSHA. Note: This module includes materials mandated by Cal/OSHA
- What this Cal/OSHA training means to you
- Employee’s rights under Cal/OSHA
- Employer’s responsibilities under Cal/OSHA
- Types of Cal/OSHA standards and how they are organized
- How Cal/OSHA inspections are conducted
- Internal and external resources you can rely on for help
Safety and Health
- Safety and health programs within the workplace
- Management leadership and employee involvement
- Workplace analysis
- Hazard prevention and control
- Safety and health training
- Job safety analysis
- Ergonomics — definition, risk factors in the employee and the task
- Controlling ergonomic risk factors
- Workplace violence
Record Keeping and Reporting
- Reporting procedures to follow for deaths or multiple hospitalizations
- Exceptions
- Record keeping 29 CFR, part 1904, including:
- Partial exemptions for employers with 10 or fewer employees
- Partial exemptions for certain industries
- General recording criteria for:
- Needlestick and sharps injuries
- State record-keeping regulations
- Medical removal cases
- Occupational hearing loss
- Tuberculosis
- Records retention and updating
- State record-keeping regulations
Inspections, Citations and Penalties
- The inspection process — how it works, Cal/OSHA priorities and inspection results
- Employer options after an Cal/OSHA inspection
- The different types of violations
- Penalties
- Penalty abatement factors
- Posting requirements
- How to contest citations after an inspection
- Follow-up inspections and failure to abate
- Employer discrimination
- Providing false information
Walking and Working Surfaces
- Guarding holes as well as floor and wall openings
- Fixed industrial stairs
- Ladders: portable metal, wood and fixed
- Safety requirements for scaffolding
- Manually propelled mobile ladder stands and scaffolds
- Other working surfaces
- Fall Protection in General Industry
First Aid
- Emergency eye washes and showers
- First aid trained first responders
Bloodborne Pathogens
- Elements of a successful exposure control plan
- Communication of hazards to employees through signs and labels
- How to determine an employee’s exposure
- Needles
- Sharps disposal containers
- Personal Protective Equipment (PPE)
- Universal precautions and general safe work practices
- Housekeeping
- Immunization and post-exposure follow-up program
Personal Protective Equipment
- Scope, application and definitions
- Protection of eye and face
- Respiratory protection
- Head protection
- Foot protection
- Hand and body protection
- Lifesaving equipment
- Personal fall arrest systems
- Positioning device systems
Materials Handling and Storage
- General materials handling
- Putting together a powered industrial truck training program
Permit-Required Confined Spaces
- Non-permit spaces
- Permit-required spaces
- General requirements
- Required forms of warning
- Written entry permit program
- Pre-entry atmospheric testing
- Required ventilation
- Safe permit space entry operations
Lockout/Tagout
- Purpose, scope and application of a lockout/tagout program
- Materials and hardware: lockout/tagout devices, requirements and criteria
- Application of energy control devices
- Basic steps in controlling energy
- Preparing for shutdown
- Shutting down machinery and equipment
- Applying and removing lockout/tagout devices
- Verifying machinery or equipment isolation
- Basic steps for release from lockout/tagout
- Inspection of machinery and equipment
- Positions affected and other workers
- Remove lockout/tagout devices
- Release after long-term shutdown
- Contractors, group lockout/tagout and shift changes
- Employee training and communication
- Evaluating written energy-control procedures
- Reviewing lockout and tagout procedures
Machine Guarding
- General requirements for all machines
- Abrasive wheel machinery
- Mechanical power presses
- Hand and portable powered tools and other hand-held equipment
- Welding, cutting and brazing
- Oxygen-fuel gas welding and cutting, arc welding and resistance welding
Hearing Conservation
- Required monitoring of occupational noise exposure
- Required audiometric testing
- Required hearing protection
- Exposure and testing records retention
- Accident and incident investigation
- Types of investigations, investigative techniques and investigative procedures
Hazardous Materials
- Flammable and combustible liquids
- Compressed gases
- Safety management of highly hazardous chemicals
- Hazardous waste operations and emergency response
Exit Routes, Emergency Action Plans, Fire Prevention Plans and Fire Protection
- Fire prevention plans and detection systems
- Employee alarm systems
- Fire Brigades
- Portable fire extinguishers
- Standpipe and hose systems
- The minimum elements of an emergency action plan
- Exit routes
Electrical
- Electric utilization systems
- General requirements
- Wiring design and protection
- Wiring methods, components and equipment
- Specific purpose equipment and installations
- Hazardous (classified) locations
- Special systems
- Selection and use of work practices
- Use of equipment
- Safeguards for personnel protection
Hazard Communication
- Purpose of the standard
- Hazard assessment
- Elements and accessibility of the written plan
- Hazardous chemical inventory listing
- Safety Data Sheets (SDS)
- Labeling
- Training
- Hazard assessment for non-routine tasksv
- Work performed by outside contractors
- Non-labeled pipes
- Records retention